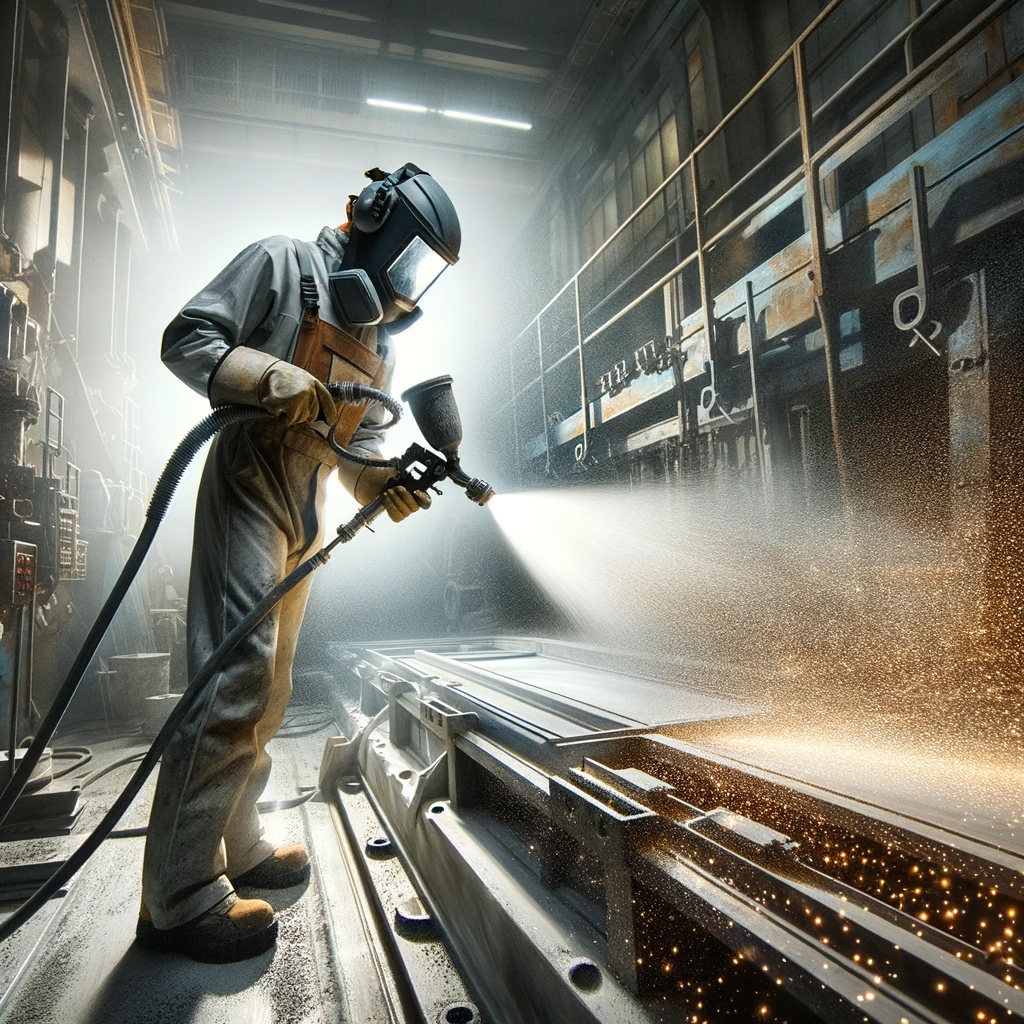
In the world of industrial manufacturing, abrasive technology plays a pivotal role in shaping, cutting, and polishing materials for a variety of applications. The industry has evolved significantly over the years, and today it offers advanced tools and materials that increase efficiency, safety, and performance. This blog post delves into the world of abrasive industrial, exploring its techniques, applications, and future trends.
What Is Abrasive Industrial?
Abrasive industrial refers to the use of abrasive materials to modify the surface of various products. This process involves the use of grinding wheels, sanding belts, polishing discs, and other tools to shape, finish, and clean different materials. Abrasives can be natural, like diamond or garnet, or synthetic, like aluminum oxide or silicon carbide.
Key Applications of Abrasive Technology
Abrasive industrial has numerous applications across various industries. Here are some of the key areas where abrasive technology is indispensable:
Metalworking: Abrasive tools are essential in metal fabrication, welding, and machining processes. They help cut, grind, and polish metals to create precision parts and components.
Woodworking: In the woodworking industry, sanding belts and discs are used to smooth wood surfaces, remove imperfections, and prepare wood for finishing.
Glass and Ceramics: Cutting and shaping glass and ceramic materials require the use of abrasives to achieve clean, precise edges and smooth surfaces.
Automotive: Abrasive materials play a key role in auto body repair, paint preparation, and finishing processes.
Electronics: The electronics industry relies on abrasives for surface treatment, cleaning, and deburring of intricate components.
Trends and Innovations in Abrasive Industrial
The abrasive industry is constantly evolving, driven by the need for improved performance, safety, and sustainability. Here are some of the latest trends and innovations:
Advanced Materials: New abrasive materials such as ceramic alumina and superabrasives like CBN (cubic boron nitride) offer enhanced durability and efficiency.
Precision Manufacturing: Advances in abrasive tools and machines allow for highly precise and automated processes, reducing material waste and improving consistency.
Eco-Friendly Solutions: There is a growing focus on developing abrasives that are environmentally friendly and reduce pollution.
Digital Integration: The industry is increasingly integrating digital technologies such as IoT sensors and data analytics to optimize abrasive processes.
Conclusion
Abrasive industrial plays a crucial role in modern manufacturing, enabling precision and efficiency across multiple industries. As technology continues to advance, the abrasive industry is poised for exciting growth and innovation.