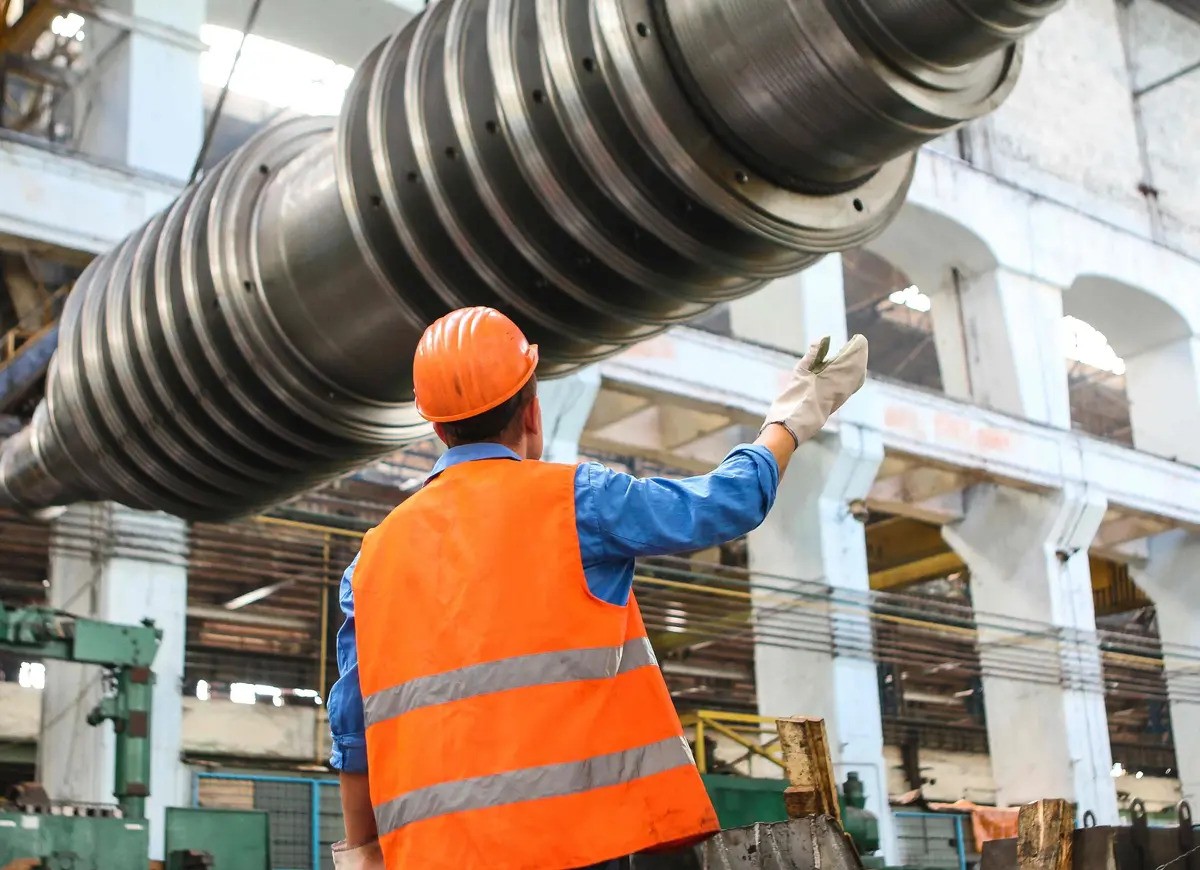
Corrective maintenance is a fundamental aspect of the overall maintenance strategy for any organization that relies on equipment and machinery. Unlike preventive maintenance, which is scheduled and proactive, maintenance is performed after a fault or failure has been detected. This blog post delves into the importance of corrective maintenance, outlining its benefits, challenges, and best practices for implementation.
What is Corrective Maintenance?
Corrective maintenance, also known as repair maintenance, involves the identification, isolation, and rectification of a problem that causes a system or equipment to fail to perform optimally. It is typically reactive, as it occurs after the equipment has already shown signs of malfunction.
The Role of Corrective Maintenance in Industry
Immediate Problem Solving: Corrective maintenance addresses failures as they occur, ensuring minimal downtime and disruption to operations.
Cost Efficiency: In certain scenarios, maintenance can be more cost-effective than preventive measures, especially for less critical equipment.
Flexibility: This maintenance strategy allows for flexible management of maintenance resources since actions are taken as needed rather than on a set schedule.
Benefits of Effective Corrective Maintenance
Implementing an effective corrective maintenance strategy can lead to several benefits:
Reduced Downtime: Quick fixes reduce the downtime associated with malfunctioning equipment.
Increased Equipment Life: Proper repairs can extend the life of equipment.
Enhanced Safety: Immediate corrective actions can prevent hazards associated with equipment failure.
Challenges in Corrective Maintenance
While corrective maintenance is essential, it comes with its set of challenges:
Unpredictability: The unexpected nature of failures can lead to abrupt halts in production.
Higher Long-Term Costs: Frequent breakdowns can lead to higher costs over time if not managed properly.
Resource Allocation: Efficient resource allocation becomes crucial, as unplanned maintenance can strain resources.
Best Practices for Corrective Maintenance
To overcome these challenges and harness the benefits of corrective maintenance, consider the following best practices:
Thorough Documentation: Keep detailed records of all maintenance activities to identify recurring issues and improve future maintenance plans.
Skill Development: Ensure that maintenance personnel are well-trained and equipped with the necessary skills to handle complex repairs.
Use of Technology: Implement maintenance management software to track equipment status, and maintenance history, and to schedule urgent repairs promptly.
Case Studies: Successful Corrective Maintenance
Manufacturing Plant Turnaround: A manufacturing facility implemented a streamlined corrective maintenance process that reduced machine downtime by 30%.
Utility Company Response: After adopting advanced diagnostic tools, a utility company was able to quickly identify and correct issues, improving service reliability by 25%.
Integrating Corrective with Preventive Maintenance
The most effective maintenance strategy combines elements of both preventive and corrective maintenance. By integrating these approaches, organizations can not only fix issues promptly but also anticipate and prevent potential failures.
Regular Inspections: Even within a corrective maintenance framework, regular inspections can help identify potential failures before they become critical.
Predictive Maintenance Techniques: Incorporating predictive tools, like vibration analysis and thermal imaging, can help in transitioning from purely corrective to a more predictive maintenance approach.
Conclusion
Corrective maintenance as well as breakdown maintenance is an essential component of any maintenance strategy. It requires a balanced approach and integration with other maintenance types to ensure operational efficiency and equipment reliability. By understanding its role, benefits, and challenges, organizations can significantly improve their maintenance operations and overall productivity.
Understanding and implementing complete maintenance effectively is crucial for any organization that depends on machinery and equipment. With the right strategies and tools, it is possible to not only repair but also prevent future issues, ultimately leading to a more reliable and efficient operation.