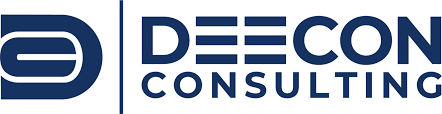
A Quality Management System (QMS) is a structured framework that outlines the processes, procedures, and responsibilities required to achieve quality policies and objectives. It serves as a blueprint for maintaining and improving the quality of products and services, ensuring that they meet customer expectations and regulatory requirements.
The Importance of a Quality Management System
Implementing a QMS is essential for any organization seeking to enhance customer satisfaction, streamline operations, and reduce waste. By systematically managing quality, businesses can achieve consistency in their outputs, reduce the risk of defects, and improve overall efficiency. This not only boosts customer trust and loyalty but also provides a competitive edge in the market.
Key Components of a Quality Management System
A robust QMS typically includes several key components:
- Quality Policy: A statement that defines the organization’s commitment to quality and sets the direction for quality objectives.
- Quality Objectives: Specific, measurable goals aligned with the quality policy.
- Process Management: Identification and management of processes to ensure they produce the desired outcomes.
- Document Control: Procedures for managing documents and records to ensure their accuracy and availability.
- Internal Audits: Regular reviews of the QMS to assess its effectiveness and identify areas for improvement.
- Continuous Improvement: Ongoing efforts to enhance processes and performance.
Benefits of Implementing a Quality Management System
The advantages of a QMS are manifold. Organizations can expect improved product quality, higher customer satisfaction, and enhanced operational efficiency. Additionally, a well-implemented QMS helps in complying with regulatory standards, reducing the risk of non-compliance penalties. It also fosters a culture of continuous improvement, encouraging employees to identify and implement enhancements in their daily activities.
Steps to Develop a Quality Management System
Developing a QMS involves several critical steps:
- Define the Quality Policy and Objectives: Establish clear, achievable quality goals.
- Identify Key Processes: Map out the essential processes that impact product or service quality.
- Document Procedures: Create detailed documentation for each process, including instructions, responsibilities, and performance metrics.
- Implement the QMS: Roll out the QMS across the organization, providing necessary training to employees.
- Monitor and Measure Performance: Use performance indicators to track the effectiveness of the QMS.
- Conduct Regular Audits: Schedule periodic audits to review the QMS and ensure compliance with established standards.
- Drive Continuous Improvement: Encourage ongoing feedback and make adjustments to enhance the QMS.
Challenges in Implementing a Quality Management System
While the benefits are significant, implementing a QMS can pose challenges. These may include resistance to change from employees, the complexity of documenting and standardizing processes, and the need for ongoing training and development. Organizations must be prepared to address these challenges through effective communication, leadership support, and a commitment to fostering a quality-centric culture.
Conclusion
A Quality Management System ISO 9001 is a vital tool for any organization aiming to achieve high standards of quality and operational excellence. By systematically managing quality, businesses can not only meet customer and regulatory requirements but also drive continuous improvement and gain a competitive advantage. Despite the challenges involved, the long-term benefits of a robust QMS make it a worthwhile investment for any organization committed to excellence.