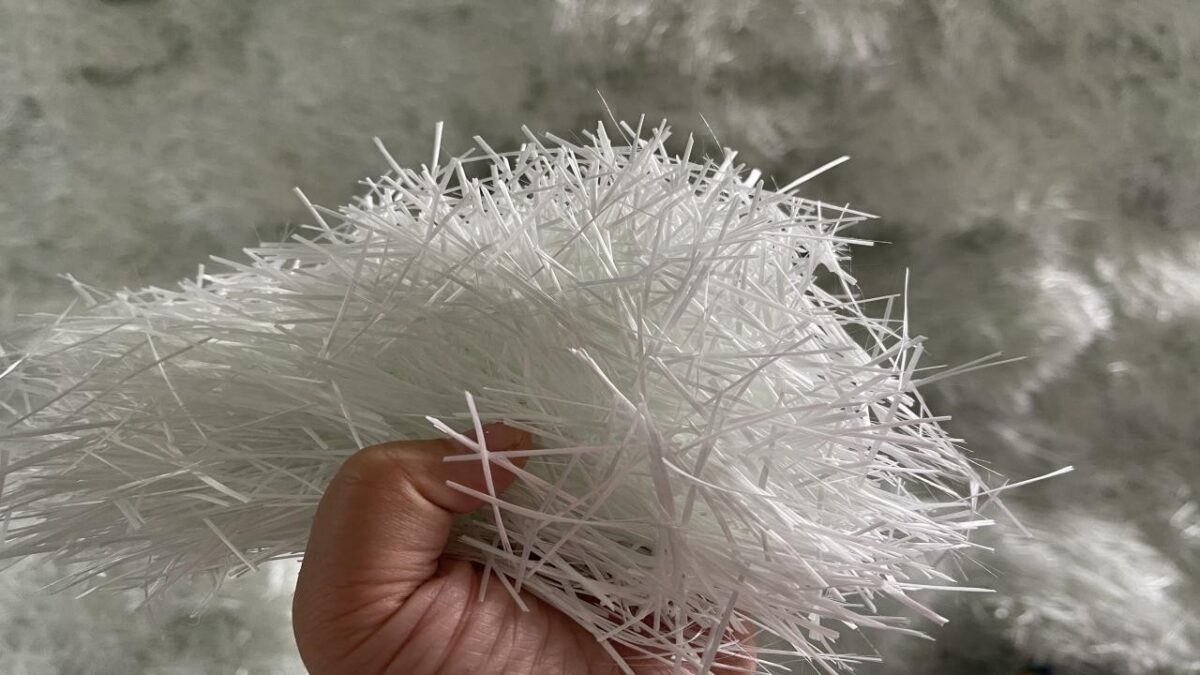
The new entry to the sky was high-strength chopped glass fiber, earning fame because of its excellent attributes. High-performance composite materials exhibit excellent mechanical qualities, good thermal resistance, and desirable impact absorption. This increasing use of high-strength chopped glass fiber in automobile components involves mostly weight-saving strategies and the consequent improvement of fuel usage and safety.
Enhanced Strength and Durability
High-strength chopped glass fiber greatly enhances the structural robustness of parts in automobiles. Unlike steel or aluminum as traditional materials, chopped glass fiber gives superior tensile strength but is very lightweight. Such properties allow the various components of vehicles to withstand stresses and impact without sacrificing service life.
In addition, chopped-glass fiber reinforcement allows plastics or composites to resist crack and deformation, increasing product lifetimes, and hence cutting down on repair and replacement. Car designers enjoy low maintenance and high reliability, thus winning greater consumer satisfaction in return. High-strength chopped glass fiber plays a well-defined role in imparting robustness to modern vehicles, be it body panels, engine covers, or structural reinforcements.
Weight Reduction for Improved Fuel Efficiency
One of the most important goals for automotive designers is weight reduction since lighter vehicles have lower fuel consumption and also generate lower emissions. Very importantly, chopped glass fiber helps gain significant weight by replacing heavier metals using lightweight, strong, yet durable composites instead. This change benefits the manufacturers in their efforts to develop fuel-efficient cars with strict compliance, regarding environmental regulations.
This underwritten weight of the vehicle results in improved overall performance in areas such as acceleration, handling, and braking as a direct effect of chopped glass fiber. Also, it yields very favorable results for electric vehicles (EVs). Reduced use of energy in its operation eventually minimizes the footprint of carbon emissions from transportation. Less energy is required for using lightweight automobiles. Most important for EVs is the increase in battery life and improved range that can be achieved through this light material. Such vital features make high-strength chopped glass fiber a revolutionary option for many demands concerning sustainability as a driving force toward the future.
Improved Impact Resistance and Safety
Vehicle safety is one of the highest concerns for the manufacturers as well as the consumers. The aforementioned property imparts a better resistance against impacts of the high-strength chopped glass fibers, thus imparting increased crash performance to automobiles. When used in the structural components and body panels, it would help absorb and dissipate energy that occurs in case of collision, thus minimizing damage to the structure and protecting passengers.
This new material appears to be very useful in the function of other crucial safety components, for example, bumpers and side panels. Unlike traditionally manufactured metals, which deform on impact, composites reinforced by chopped glass fiber retain their shape, reducing the chances of severe injuries. Moreover, just like being lightweight, it allows more balanced weight distribution, thus increasing vehicle stability and improving the risk of a rollover during severe impacts.
Corrosion and Chemical Resistance
Corrosion and chemical degradation are two of the biggest disadvantages of conventional automotive materials. It is well known that metals, in particular, steel, rust when moisture, road salts, and other chemicals take part in degrading the surface of metal. High-strength chopped glass fiber, on the other hand, has a very insignificant response to corrosion and does not get compromised even under rough environmental conditions. It is this quality that allows it to be applied in many use cases in the car: from hood components to battery enclosures and parts of fuel systems. It is possible to produce vehicles that last longer and require less maintenance by the use of chopped glass fiber composites.
Enhanced Design Flexibility
High-strength chopped glass fiber provides unprecedented freedom and latitude for design. Whereas metals will be limited in the shaping and forming of parts, fiber-reinforced composites can be easily formed to fit complex geometries. Thus, designers can create astonishingly aerodynamic, lightweight, and beautiful components for the vehicle, which may have been virtually impossible with traditional materials.
Furthermore, the benefit of thermoplastic and thermoset resin integration into chopped glass fiber lies in customizing a part for strength and rigidity or texture. This property is heavily relied upon in interior design elements such as dashboards, door panels, and seating structures, where strength and beauty work hand in hand.
The End
High-strength chopped glass fiber has changed dynamics in the automobile world. It provides strength, properties of durability, and lightweight considerably beyond most common materials in the industry. Numerous benefits offered in addition to the highlighted include impact resistance, corrosion resistance, flexibility to design, and cost-effectiveness, among others. High-strength chopped glass fiber would be an appropriate material for modern vehicle manufacturing. It would be beneficial also for fuel economy and environmental sustainability according to the prospects of the industry, thus demanding greener and more energy-efficient transport solutions.